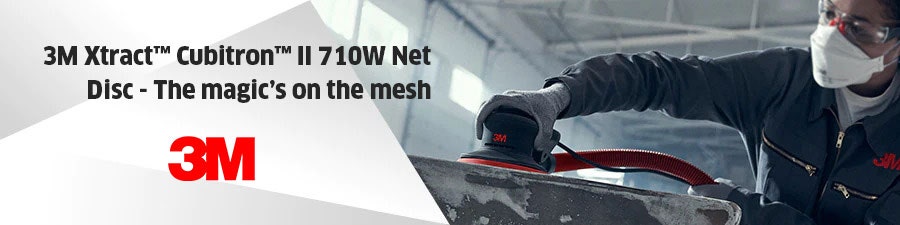
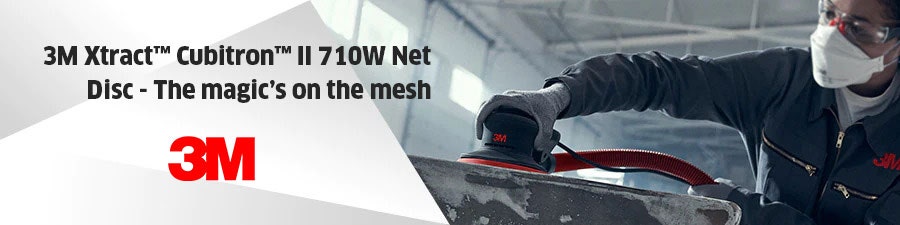


The magic’s on the mesh – giving you twice the cut rate, twice the disc life … and up to 99% dust free sanding.
3M’s scientists have created the most technically advanced abrasive disc setting new standards for the most important performance parameters of a sanding disc - cut rate, disc life, finish consistency and dust extraction.
Our proprietary abrasive technologies have been brought together in a unique way for the first time to give unmatched performance in one single abrasive.
Two revolutionary elements have created the magic on the mesh
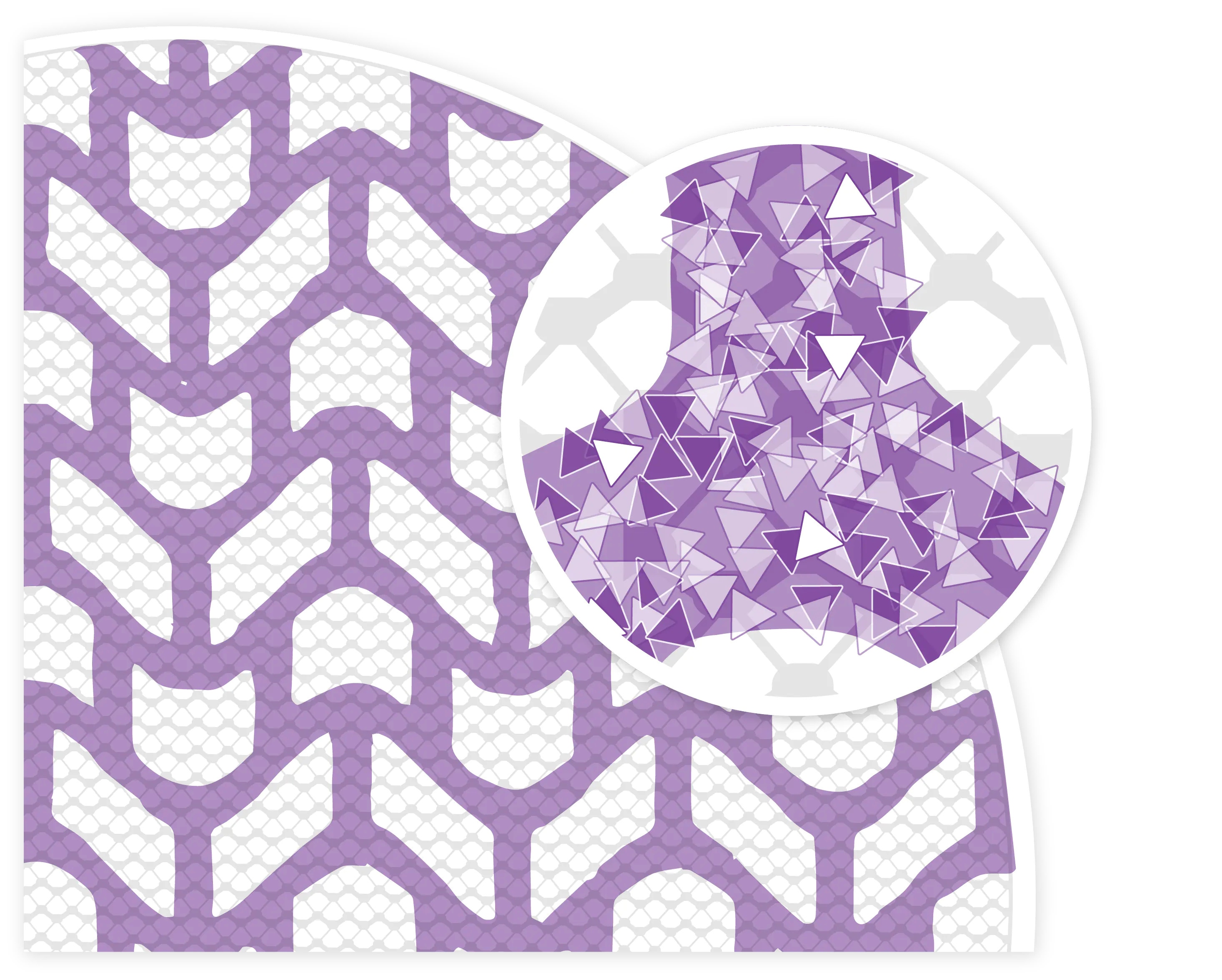
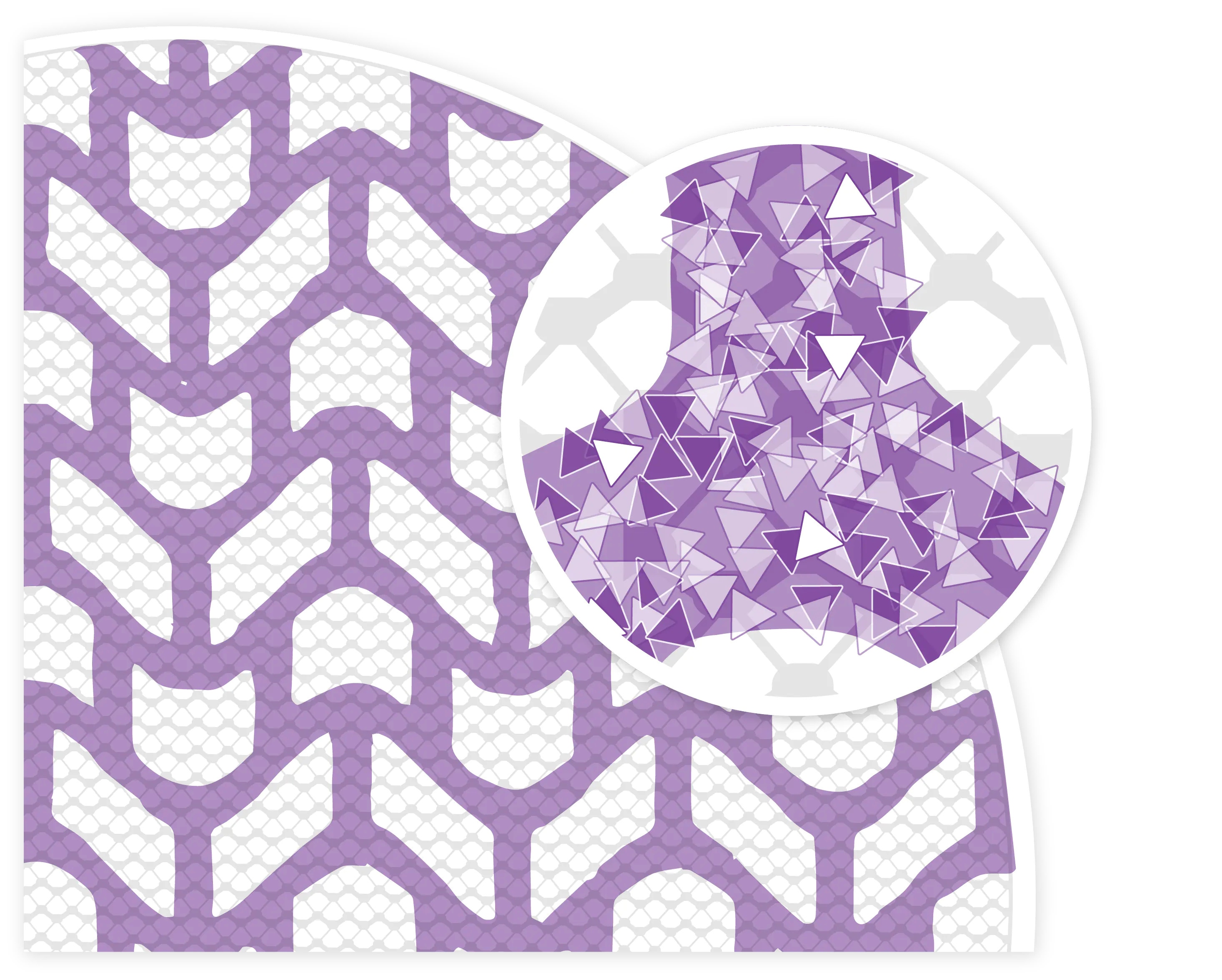
1) 3M™ Precision-Shaped Grain
Developed using microreplication technology, 3M’s legendary precision-shaped ceramic grain self sharpens. As each identical triangular shaped grain wears, it continually fractures to form sharp points, which seamlessly and evenly, cut through any substrate and runs cooler too – unlike standard ceramic crushed grain.
2) Unique disc pattern
The distinctive pattern increases the pressure of the disc to give a significantly higher cut rate, requires less operator pressure and enables exceptional dust extraction from the substrate.
Together these technologies enable you to sand at twice the speed, virtually dust free, and increase disc life by fifty percent - increasing your productivity and reducing costs
5-Point Sanding Productivity Matrix
Introduction
In manufacturing, productivity is one of the key measures of success. In fact, the core purpose for you and other manufacturers is to be as productive as possible; to produce enough goods to meet customer demand and grow.
For every business, regardless of market or sector, the pressure is therefore always on to boost productivity. This is where efficiency comes in: optimal performance through streamlining processes - and it’s this balance of productivity and efficiency that businesses should strive for.
There’s a wide range of ways to improve manufacturing productivity, particularly through tooling and machinery, processes and people. But it can also be found in areas of the business that might not be that obvious.
For example - your sanding consumables which can often be perceived as not able to have a material impact on productivity gains.
We’ve spent thousands of hours listening to the challenges and needs of customers across Europe and in almost every sector. From this we’ve developed 5 pillars of sanding productivity. These are the key elements that can help revolutionise your sanding process - improving productivity, quality, cost and health and safety.
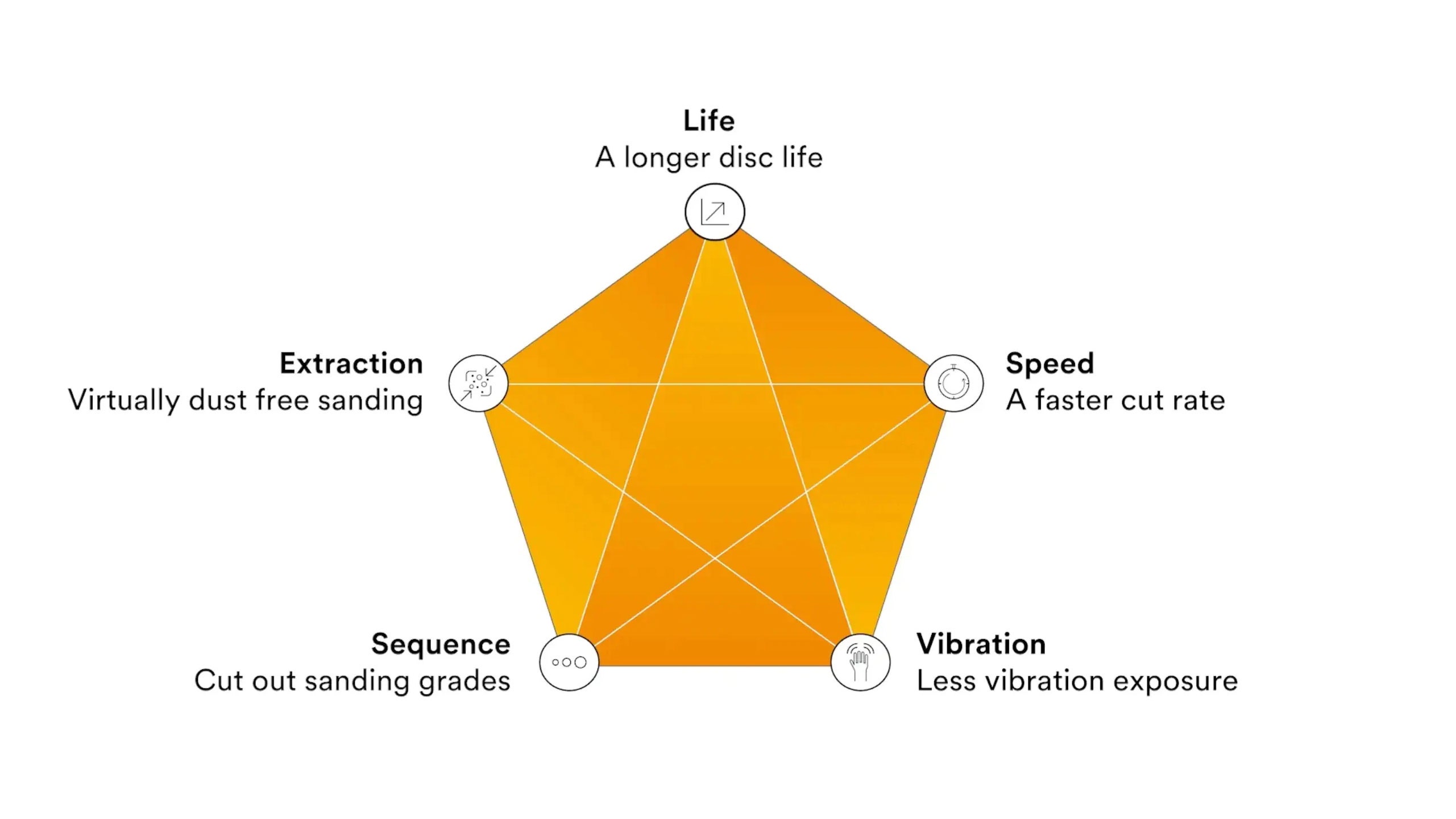
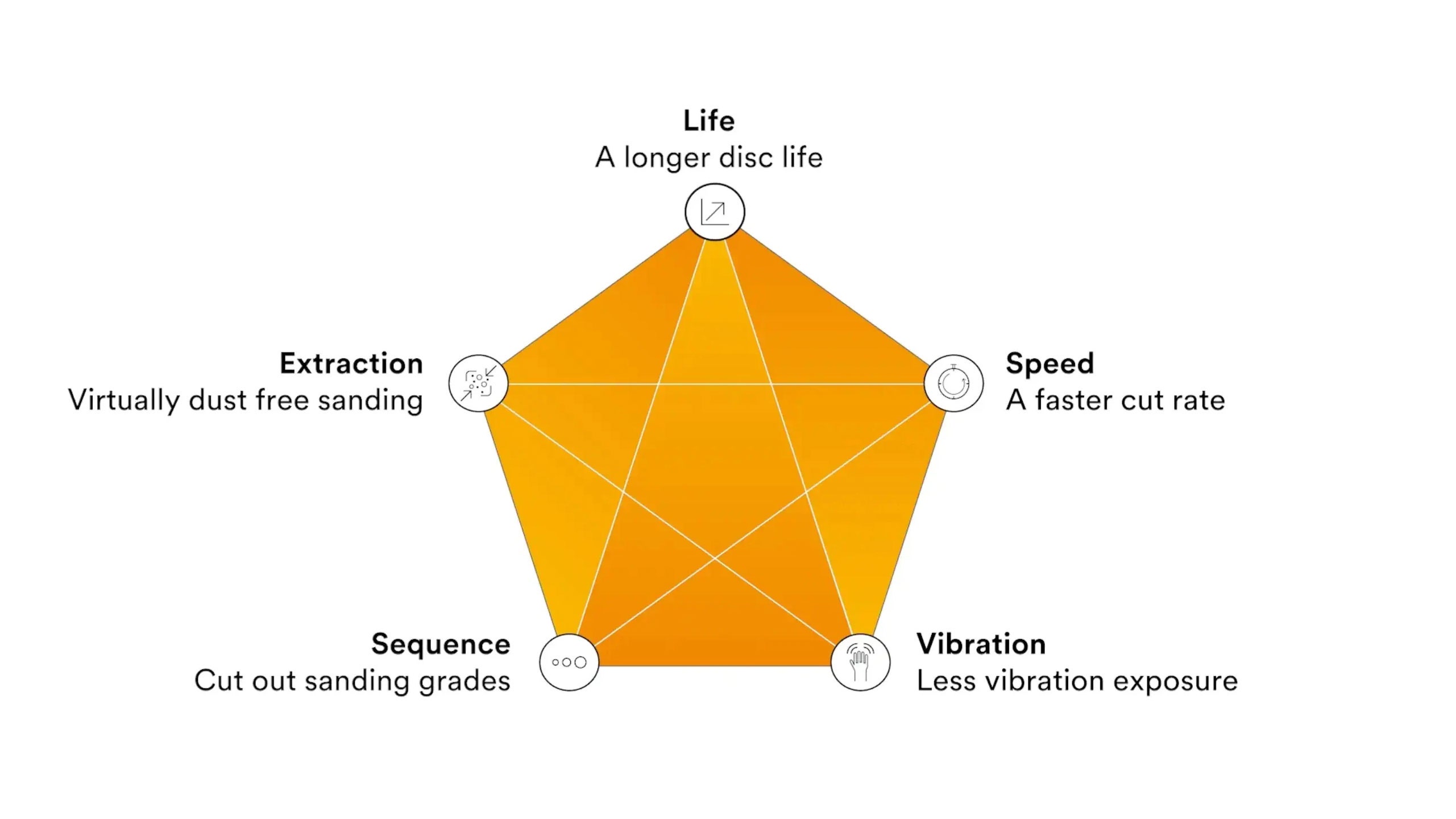
Life - A longer disc life
The benefits of longer disc life are fewer disc changeovers, which means less downtime for operators. That’s less time getting the disc, replacing one for another, lining it up and re-starting the job.
The main benefit however is lower disc consumption. This means a lower consumable cost per part made. And provided the disc price is proportionally lower than the difference in life – you get a reduction in overall abrasive consumable spend.
Conclusion: when it comes to these consumables, the key evaluation, should be disc cost per part (or parts) sanded.
Have a look at our demo video on disc life and durability of the 3M Xtract™ Cubitron™ II 710W Net Discs.
Speed - A faster cut rate Vibration - Less vibration exposure
Speed has a significant productivity impact, but importantly with vibration being considered as well, a health and safety one too. Many people don’t realise that orbital sanders in general have significantly higher vibration levels than an angle grinder due to their dual action as opposed to the rotary action of a grinder.
Let’s look at speed first.
Clearly the benefit of a faster sanding disc is more parts get sanded in less time. If you’re working in an environment where the amount of parts to sand is unlimited, then you’ll get more parts done in a shift. This helps free up bottlenecks, helps cope with production capacity constraints and therefore increases overall manufacturing productivity. If the number of parts you’re sanding is limited, then you will get those parts done quicker. This means you can free up operators to work on something else, after all sanding is not considered a very pleasant job to be done in the workshop.
Focusing now on vibration exposure.
Let’s focus on the principle that using a faster cutting disc means less vibration is produced in the same period of time. There’s a 1:1 relationship between time sanding and vibration exposure, whatever disc you are using. If you sand for half the time… you will halve the vibration. HAVS is a painful and disabling disorder. It’s highly preventable, but once the damage is done, it’s irreversible. So to be able to sand more parts without impacting worker health and safety in anyway is a huge benefit. If you’re sanding limited parts during an 8 hour shift, then the benefit is that operatives are exposed to less vibration. In all, it’s a double win for your business and the sanding operators themselves.
Extraction - Virtually dust free sanding
Let’s now talk about the final pillar in our productivity matrix - Extraction.
With mesh sanding discs, the industry perception is there’s a trade-off between disc performance and dust extraction, but we can show this isn’t always the case. It’s vital that you have a well-functioning tool and extraction system working alongside a disc with high extraction capability for this to be a reality in your workplace.
Putting in words how well the Xtract System performs on dust extraction would not do it justice. We've made use of this cool tool called "The Vortex" to really highlight the performance level. Let's have a look at our demo video on dust extraction. See for yourself!